ball mill c ramique porcelaine ball mill
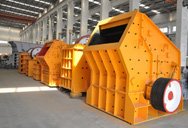
On the Use of Ball Milling for the Production of Ceramic
2015.7.9 Read this article. In the present research work, the mixture of boron carbide and graphite ceramic powders with a theoretical composition of 50% each by weight
More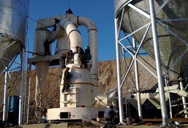
(PDF) On the Use of Ball Milling for the Production
2015.4.22 PDF In the present research work the mixture of boron carbide and graphite ceramic powders with a theoretical composition of
More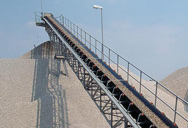
Can ceramic balls and steel balls be combined in an
2022.11.1 Abstract Recent research contends that ceramic balls significantly reduce energy consumption in industrial tumbling mills. In this work, the binary media method is
More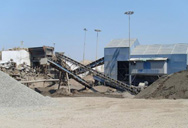
Modeling of the planetary ball-milling process: The case
2016.8.1 A numerical dynamic-mechanical model of a planetary ball-mill is developed to study the dependence of process efficiency on milling parameters like ball size and
More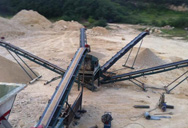
Ball milling: a green technology for the
Abstract Ball milling is a simple, fast, cost-effective green technology with enormous potential. One of the most interesting applications of this technology in the field of cellulose is the preparation and the chemical
More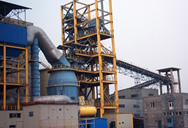
A Comparison of the Fine-Grinding Performance
2022.8.11 effect of ceramic balls and cylpebs on the fine-grinding performance of wet tumbling mills has not yet been systematically studied. The main purpose of this
More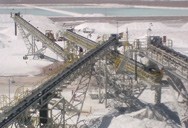
Calculation method and its application for energy
existing research focuses on the ball mills used for ore and cement processing. There is little research on the energy consumption of ball mill in the ceramic industry.
More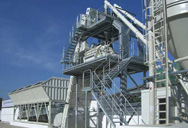
Nanoceramics from the Ball Mill Interceram - International Ceramic
69 , 17 ( 2020 ) Download PDF Interceram - International Ceramic Review 1163 Accesses Explore all metrics Cite this article Chemists at the Max Planck Institute for Coal
More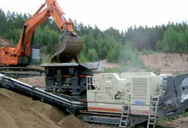
China Ceramic Ball Mill, Ceramic Ball Mill Wholesale,
China Ceramic Ball Mill wholesale - Select 2024 high quality Ceramic Ball Mill products in best price from certified Chinese Ceramic manufacturers, Ceramic Product suppliers,
More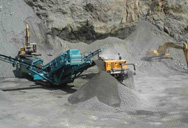
UG编程的创建加工刀具的方法和步骤 - 知乎
2019.8.17 1.打开UG软件,点击“文件”,接着点击“新建”,再设置一个保存文件的路径和文件的名称,然后点击“开始”,再点击“加工”,在弹出的窗口中,按照默认的CAM会话配置的“cam _ general”,再把要创建的CAM
More
行星式球磨仪PM100--德国RETSCH(莱驰)研磨仪粉
Download. The Planetary Ball Mill PM 100 is a powerful benchtop model with a single grinding station and an easy-to-use counterweight which compensates masses up to 8 kg. It allows for grinding up to 220 ml
More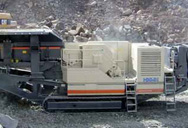
Ball Mill: Operating principles, components, Uses,
2022.11.30 A ball mill also known as pebble mill or tumbling mill is a milling machine that consists of a hallow cylinder containing balls; mounted on a metallic frame such that it can be rotated along its longitudinal axis.
More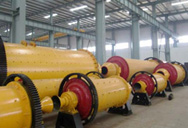
A Review of the Grinding Media in Ball Mills for Mineral
2023.10.27 The ball mill is a rotating cylindrical vessel with grinding media inside, which is responsible for breaking the ore particles. Grinding media play an important role in the comminution of mineral ores in these mills. This work reviews the application of balls in mineral processing as a function of the materials used to manufacture them and the
More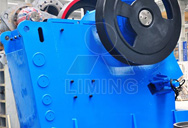
Quantifying the energy efficiency of fine grinding circuits
2021.11.25 In the first survey the ball mill was underperforming due to the low density in the mill, which was rectified in the second survey. The ball mill was grinding to a P 80 of 50 to 70 µm, therefore the traditional marker size (75 µm) was not applicable, and this can be seen by the increase in SSE for coarser sizes as the marker size approached P ...
More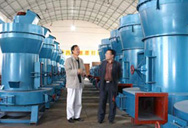
Ball Milling in Organic Synthesis: Solutions and Challanges
2011.3.2 It is rather recommend changing reaction time than frequency. Start with 75-100% of the maximal operation frequency of the ball mill. The thermal stress for the reactants could be reduced by using cycled mode: mill for a. specific amount of time – 5-10 min pause – start milling again and repeat the procedure for the required amount of time.
More
Ball milling as an important pretreatment technique in
2021.8.12 The load exerted by grinding balls on lignocellulosic biomass in a vibratory ball mill is significantly larger than the other mill types, resulting in the highest enzymatic hydrolysis yield. The glucose yields achieved were 95.2, 75.2, 61.0, and 52.8%, for vibratory ball mill, tumbler ball mill, jet mill, and centrifugal mill, respectively ...
More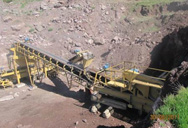
Ball Mill Balls - Manufacturing Of High Quality Ball Mill Ball
Ball mill balls. Ball mill balls are a type of ball used in ball mills, usually made of high-hardness materials such as steel, ceramics, hard alloys, etc. Ball mill steel balls is an important part of the ball mill, its main function is to carry out the grinding operation in the ball mill, and the material is crushed into the required size.
More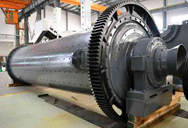
Ball-milling: A sustainable and green approach for starch
2023.5.15 Ball-mills are categorized into four types depending on the motion generated to produce momentum in grinding balls and act upon the material with various milling forces. These are planetary, tumbling, vibratory, and attrition mills. 3.1. Planetary ball mill. Planetary ball mills are simple and efficient in producing ground/pulverized material.
More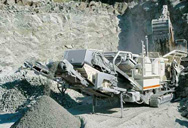
Energy-Efficient Technologies in Cement Grinding IntechOpen
2016.10.5 The energy consumption of the total grinding plant can be reduced by 20–30 % for cement clinker and 30–40 % for other raw materials. The overall grinding circuit efficiency and stability are improved. The maintenance cost of the ball mill is reduced as the lifetime of grinding media and partition grates is extended. 2.5.
More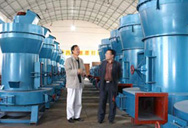
Ball Milling in Organic Synthesis: Solutions and Challanges
2011.3.2 It is rather recommend changing reaction time than frequency. Start with 75-100% of the maximal operation frequency of the ball mill. The thermal stress for the reactants could be reduced by using cycled mode: mill for a. specific amount of time – 5-10 min pause – start milling again and repeat the procedure for the required amount of time.
More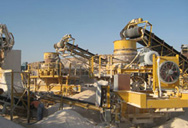
(PDF) Study on the influence of liner parameters on the power of ball ...
2018.5.1 The impact energy of grinding ball and the moving state of medium are the direct factors that affect the grinding effect of ball mill. The structure of liner is closely related to both.
More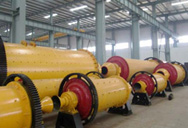
Effect of Intensive Abrasion Breakage on
2023.5.23 The secondary ball mill can increase the surface area by reducing the diameter of steel balls to enhance the abrasion. Industrial application results show that after the abrasion of the secondary ball mill
More
Ball milling as an important pretreatment technique in
2021.8.12 The load exerted by grinding balls on lignocellulosic biomass in a vibratory ball mill is significantly larger than the other mill types, resulting in the highest enzymatic hydrolysis yield. The glucose yields achieved were 95.2, 75.2, 61.0, and 52.8%, for vibratory ball mill, tumbler ball mill, jet mill, and centrifugal mill, respectively ...
More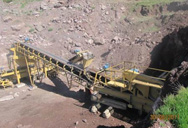
Ball Mill Balls - Manufacturing Of High Quality Ball Mill Ball
Ball mill balls. Ball mill balls are a type of ball used in ball mills, usually made of high-hardness materials such as steel, ceramics, hard alloys, etc. Ball mill steel balls is an important part of the ball mill, its main function is to carry out the grinding operation in the ball mill, and the material is crushed into the required size.
More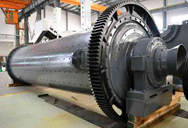
Ball-milling: A sustainable and green approach for starch
2023.5.15 Ball-mills are categorized into four types depending on the motion generated to produce momentum in grinding balls and act upon the material with various milling forces. These are planetary, tumbling, vibratory, and attrition mills. 3.1. Planetary ball mill. Planetary ball mills are simple and efficient in producing ground/pulverized material.
More
Mechanism characteristic analysis and soft measuring
2018.11.1 A mill load is defined as the instantaneous total charge of a ball mill and is composed of a new feed ore, slurry, water, and steel balls inside the mill (Tang et al., 2015a). Overloading causes “mill spitting ore,” coarsening on the particle size of mill outlet, “mill blockage,” “belly be filled full,” and production process break off.
More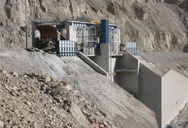
Ceramic Grinding Kinetics of Fine Magnetite Ores in the Batch Ball Mill
2023.9.10 However, when ground with ceramic balls at the same total weight, the breakage rate is basically around 0.20 min −1, which is close to that of steel ball grinding. Furthermore, when the feed size was larger than 0.212 mm, the average breakage rate of ceramic ball grinding was 8.41% lower than that of steel ball grinding.
More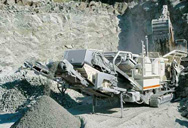
Energy-Efficient Technologies in Cement Grinding IntechOpen
2016.10.5 The energy consumption of the total grinding plant can be reduced by 20–30 % for cement clinker and 30–40 % for other raw materials. The overall grinding circuit efficiency and stability are improved. The maintenance cost of the ball mill is reduced as the lifetime of grinding media and partition grates is extended. 2.5.
More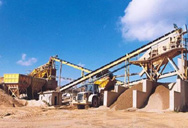
Producing Metal Powder from Machining Chips Using Ball
2023.6.27 A ball mill is additionally utilized to grind and combine materials, commonly with spherical or cylindrical-shaped grinding media such as balls or rods . Numerous researchers have effectively used ball milling to produce nanostructures of various materials or to investigate structural changes in materials during ball milling [87,88,89,90,91 ...
More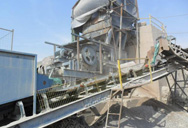
Ball Mill at Thomas Scientific
High-energy ball mill that accommodates sample sizes ranging from 0.2 - 10 grams. Ideal for grinding dry, brittle samples, mechanical alloying, slurry grinding, blending powders, and mixing emulsions. Typical samples include rocks, minerals, sand, cement, slag, ceramics, catalyst supports, glass,. Compare this item.
More
Physical Bauxite Processing: Crushing and Grinding of Bauxite
2022.1.23 In this case the grinding circuit comprises an open circuit rod mill followed by a closed-circuit ball mill. The ball mill is most often closed over a classifier like a hydro cyclone (Fig. 3.11) or DSM style screen with a fine cut of 1–1.5 mm. The course material is returned to the ball mill feed and the fine screen underflow reports to the ...
More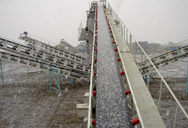
Retsch : 粉碎设备 : 球磨仪 : PM 400
行星式球磨仪 PM 400. The PM 400 is a robust floor model with 4 grinding stations and accepts grinding jars with a nominal volume from 12 ml to 500 ml. It processes up to 8 samples simultaneously which results in a high
More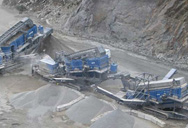
Study on shock vibration analysis and foundation
2023.1.5 When the shock force of the ball mill material is 12,500 kN, the concrete grade is C35, the shock angles are set to 10°, 20°, 30°, 40° and 50° respectively, and the dynamic responses of the ...
More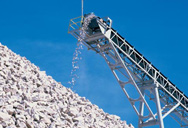
Ball milling: a green technology for the preparation and ...
The ball mill Ball milling is a mechanical technique widely used to grind powders into ne particles and blend materials.18 Being an environmentally-friendly, cost-effective technique, it has found wide application in industry all over the world. Since this mini-review mainly focuses on the conditions applied for the prep-
More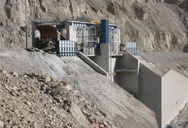
RoM BALL MILLS - A COMPARISON WITH AG/SAG
2023.12.10 SAG mills are distinguished by utilising run-of-mine (RoM) feed as grinding media with 5 – 18% steel balls added to supplement grinding media. In recent years, RoM Ball mills have started taking ...
More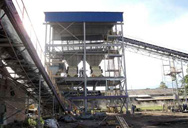
Ball Mill - an overview ScienceDirect Topics
8.3.2.2 Ball mills. The ball mill is a tumbling mill that uses steel balls as the grinding media. The length of the cylindrical shell is usually 1–1.5 times the shell diameter (Figure 8.11 ). The feed can be dry, with less than 3% moisture to minimize ball coating, or slurry containing 20–40% water by weight.
More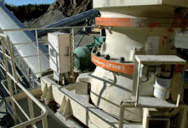
Modeling of Bauxite Ore Wet Milling for the Improvement of
2021.9.5 Several mathematical models have been developed to predict the PSDs of particulate materials, including log-normal, logistic, Gates–Gaudin–Schuhmann (GGS), and Rosin–Rammler (RR) distributions, while truncated size distributions can also be used when a particle population would have every particle smaller than a definite top size [38, 39].In
More
Autogenous Grinding Semi Autogenous Grinding Circuits
2017.7.20 Autogenous plus Ball Mill has been used very infrequently. When hard ores are encountered for extensive periods, 100 mm balls are added to the primary mill (#7). Semiautogenous-single stage. These circuits are not a good choice for many orebodies because it is not logical to expect one machine to be as efficient on 150 mm ore as it is
More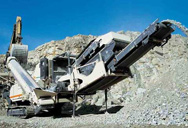
Mixer Mills - RETSCH - efficient grinding of sample volumes
Mixer Mills. Mixer mills grind and homogenize small sample volumes quickly and efficiently by impact and friction. These ball mills are suitable for dry, wet and cryogenic grinding as well as for cell disruption for DNA/RNA or protein recovery. For special applications such as mechanosynthesis, they offer unique solutions.
More