coal pulverizers and burners

Triboelectrostatic Cleaning of Coal In-Line Between Pulverizers
2022.2.22 Pulverized coal combustors are the principal means for converting coal to electricity in the United States. Coals used in these combustors have to be beneficiated
More
Coal Pulverizers - an overview ScienceDirect Topics
Coal Pulverizers. Coal pulverizers have four separate processes, all of which can be impacted by coal characteristics: drying, grinding, classification, and transport. From:
More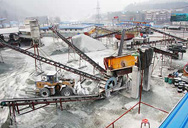
Mineral Matter Rejection In-Line Between Pulverizers
2017.8.28 In-line (between pulverizers and burners), triboelectrostatic coal beneficiation has yet to be demonstrated within a utility setting. Because no known
More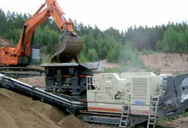
Application of plasma burners for char combustion in a pulverized coal ...
2023.9.15 Simulation II of coal combustion in corner burners with two extra plasma burners where char is combusted. In this case, both corner burners and plasma burners
More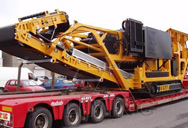
Coal pulverisers - performance and safety, IEACR/79 - ICSC
Coal pulverisers – performance and safety, IEACR/79 29 years ago David Scott This study reviews issues related to the efficient and safe operation of coal pulverising systems for
More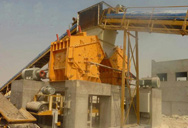
Pulverised Coal Combustion - an overview ScienceDirect
Pulverised coal (PC) combustion is the most widely used technology for utility-scale power generation in the world. In PC boilers, coal is ground into fine particles (∼100 μm) and
More
A Review of the Numerical Modeling of Pulverized Coal
2021.4.8 Abstract. High-efficiency, low-emissions (HELE) coal-fired power plant technologies operate with a higher thermal efficiency of the steam cycle for coal-fired
More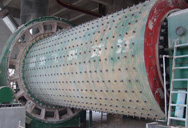
Improving Coal Pulverizer Performance and Reliability
2023.7.5 Description Pulverization is currently the favored method of preparing coal for burning. Mechanically pulverizing coal into a fine powder enables it to be burned like
More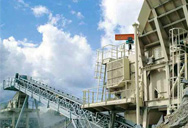
Coal Pulverizer Design Upgrades to Meet the Demands
2023.9.18 The increased use of Low NOX burners in the past 10 years has instigated a need for further development of coal pulverizer technology in an effort to ensure
More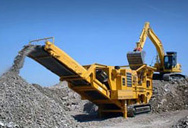
Pulverized Coal Pipe Testing and Balancing
2010.10.7 Four Steps to Fuel Line Balancing. 1. Ensure That Clean Air Balancing Is Within 2%. Balance the fuel line system resistances by clean air testing to achieve resistance within ±2% for all pipes. 2 ...
More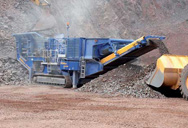
3B1 Ch 1-10 Practice Questions Flashcards Quizlet
Generally two types of draft fans are used. A _____ ____ fan supplies air to the air preheater. The preheated air for combustion goes to the coal pulverizers and to the burners. An _____ ____ fan exhausts the combustion gases from the air heater to the stack. A. center mounted, external mounted B. forced draft, induced draft C. induced draft, forced
More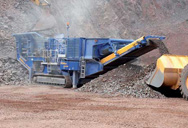
The effects of chemical pretreatment on tribocharging of
2014.2.1 Coal samples were added to the beakers respectively and the slurries were rotated by mixer. The treating time was about 3 min while the dosage of chemicals was 1000 g per ton respectively for all experiments. ... Triboelectrostatic cleaning of coal in-line between pulverizers and burners at utilities. Int. J. Coal Prep. Util., 19 (1998), pp ...
More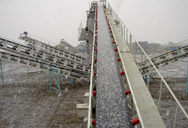
(PDF) Analysis of the Coal Milling Operations to the
2020.4.2 coal burners positioned abo ve or lowers fue l o il burners (OB). The boiler is design produc ing 100% of B MCR b y firing coal . ... Within th e pulverizers the co al is ground, dried,
More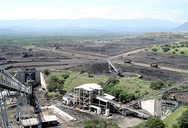
Pulverizers 101: Part I - POWER Magazine
2011.8.1 These two mill types represent perhaps 70% of the pulverizers used in modern pulverized coal plants. ... For example, if a pulverizer is operating at 100,000 lb/hr coal feed to the burners, as ...
More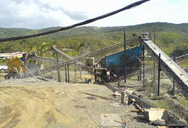
Heng Ban - University of Pittsburgh
overview. Professor Ban's research covers topics in thermal-fluid sciences, materials properties, sensors and measurement, and energy sciences. His recent focus has been to understand the relationship between material microstructural change and its thermal performance, particularly experimental and computational material thermophysical
More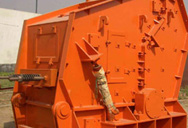
Measuring Coal Pipe Flow - POWER Magazine
2009.10.1 Combustion tuning of a pulverized coal boiler begins with balancing the air and fuel flows in the coal pipes from the pulverizers to the burners. Note that each of the coal pipes is a different ...
More
Combustion Optimization to Improve Heat Rate and Lower
2019.9.3 It has a heating value of 6,600 Btu/lb. Coal mill pulverizers process and deliver fuel to the burners. Air adjustments are made using auxiliary air dampers, as well as close-coupled overfired air ...
More
Coal Pulverizers - an overview ScienceDirect Topics
Coal Pulverizers. Coal pulverizers have four separate processes, all of which can be impacted by coal characteristics: drying, grinding, classification, and transport. ... economizer, drum, sealing systems, seal flushing systems, bearings, coal pulverizer, burners, over fire system, cleaning system, air preheaters, cooling tower, water ...
More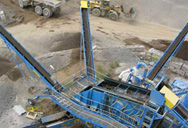
MBF Coal Pulverizers - Foster Wheeler - Yumpu
2013.4.21 We offer a full range of steam generator equipment, aftermarket products and services to the. power, industrial, and waste-to-energy sectors. Our global manufacturing and engineering network. can deliver cutting-edge products and expertise, quickly and cost competitively with best-in-class quality..
More
Pulverizers 101: Part II - POWER Magazine
2011.10.1 Pulverizers 101: Part II. Pulverizers prepare the raw fuel by grinding it to a desired fineness and mixing it with the just the right amount of air before sending the mixture to boiler burners for ...
More
Coal pulverizers: updated (Journal Article) OSTI.GOV
Abstract. In the early 1960's, Foster Wheeler introduced the first MB mill, a planetary roll pulverizer which proved to have many outstanding operational charcteristics. Among these were low power consumption, the ability to handle extremes of coal moisture, freedom from fires, and equality of coal distribution to its connected burners.
More
Triboelectrostatic Cleaning of Coal In-Line Between Pulverizers
1998.4.1 Because coal is pulverized before its combustion in PC boilers, during which time substantial mineral liberation occurs, it may be beneficial to remove mineral matter from the combustibles by using dry beneficiation techniques after the pulverizers and within the burner pipes leading to the coal burners.
More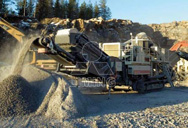
Pulverized Fuel Handling Systems: Unit, Central System, Advantages
3 天之前 The two methods used to feed the pulverized fuel to the combustion chamber of the power plant: 1. Unit System 2. Central or Bin System. In unit system, each burner of the plant in fired by one or more unit pulverizers connected to the burners, while in central system, the fuel is pulverized in the central plant and then distributed to each furnace
More
Improving Load Response and NOx Emissions with Boiler Tuning and Coal ...
2021.3.1 The Plum Point Energy Station (PPES) is a 720-MW (gross) pulverized coal-fired boiler that operates on a subcritical Rankine steam cycle with reheat. The facility is located in eastern Arkansas ...
More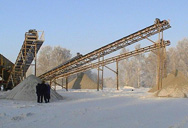
Fossil Fuel Combustion Systems - EOLSS
2017.1.16 1. Pulverized Coal Burners 1.1. Pulverized Coal Supply Pulverized coal from the coal pulverizers is conveyed in a stream of hot primary air from the mills to the burners where it is injected into the furnace space to be burned. Generally, the air–fuel ratio of the fuel mixture leaving the pulverizers is about 2:1 for
More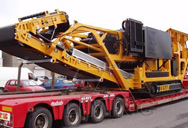
“Blueprint” Your Pulverizer for Improved Performance
2020.8.27 ablity Index (HGI), and the coal’s raw feed size and moisture content (see Figure 3 in “Finessing Fuel Fineness”). Plant operators can only improve throughput of a given mill with a particular coal (moisture and HGI are typically outside operator control) by sac-rificing fineness—by producing a coarser product for the burners.
More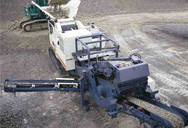
Fire and Explosion Prevention in Coal Pulverizing
2023.9.18 Proper design and operation of the pulverized coal burners protects the pulverizing system from ignition from the furnace fire. The coal/ air mixture enters the furnace through a burner nozzle at velocities in excess of the flame speed. Thus, the flame front is held stable at a distance away from the end of the nozzle where
More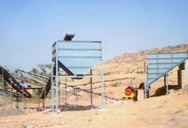
Analysis of the Coal Milling Operations to the Boiler
2021.10.28 load. From the gravimetric feeders the coal is fed into the pulverizers. Within the pulverizers the coal is ground, dried, and classified to the proper size for burning in the boiler. The primary air flow carries the fine coal to the burners, and the coarse coal falls back into the grinding zone of the pulverizer.
More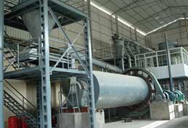
Simulation of Pulverized Coal Combustion Process
2023.3.27 In this paper, the combustion process of a 350 MW opposite pulverized coal combustion boiler is studied using a combined field test and numerical simulation. Considering the turbulence–radiation interaction (TRI) effect caused by turbulent particle pulsation during the combustion process, the TRI model is modified by introducing optical
More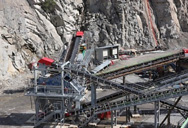
Dry separation on coal–silica mixture using rotary
2015.3.1 This study investigates the rotary triboelectrostatic separation of a fine coal and silica mixture (0.15–1 mm) to simulate the coal and silica minerals, which commonly exist in run of mine coal. The RTS with innovative designed particle charging and separation units was used to beneficiate the mixture.
More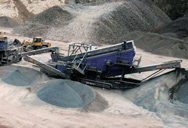
Coal Fired Power Plant Designs, Systems, and Components
2022.9.3 Coal Burners For PC units, after the coal has been pulverized, it is blown through a burner for combustion. e burner controls the now of coal and air and ignites the mixture as it enters the boiler. ere are typically four to eight burners for each pulverizer, with at least four pulverizers serv- ing a large boiler. By reducing the name ...
More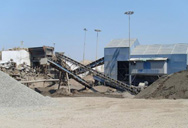
How accurate primary airflow measurements
2006.5.15 Inaccurate measurements that underestimate actual levels of primary air (PA) flow in a coal plant are particularly problematic, because higher-than-expected PA flow levels wreak havoc on more than ...
More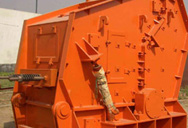
CFD analysis: bowling for pulverized coal - Power Engineering International
2009.5.1 The CFD results can be used to examine a range of geometry and flow options and increase the performance of the pulverizer. In pulverized coal fired utility boilers, control of coal fineness, and uniform distribution of coal flow from pulverizers to burners, lead directly to better control and performance of the firing system.
More
ASME PTC 4.2 - Coal Pulverizers GlobalSpec - Engineering360
Discharge coal and air piping, including valves. Motors and/or steam drives. Sources of hot air or flue gas. Figures 1 and 2 iIlustrate the arrangement of these components in pressure and suction systems for direct firing. The storage system in which the coal is pulverized and stored in bins from which it is fed to the burners as needed.
More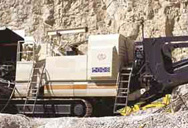
Repurposing coal-fired power plants: benefits and
2023.3.27 The entire fuel storage, reclaiming, conveyor system, coal bunkers, pulverizers, and burners can be repurposed to accommodate biomass with minor modifications. This type of conversion has been successfully implemented at utility-scale power plants. Challenges to the conversion include the high volatility of biomass fuels
More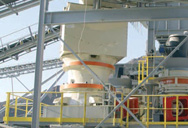
Aggregates - Pulverizers – Measur Materials Testing Equipment
Measur is North America's leading supplier of materials testing equipment, offering sales, maintenance, and on-site calibration services. We specialize in both destructive and non-destructive methods, adhering to C.S.A. and A.S.T.M. standards. Explore our website for more information or contact us today.
More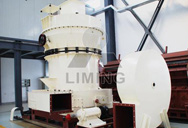
Power Plants of the Future: 21st Century Coal-Fired Steam Generator
2019.8.1 The markets for new coal-fired steam generators will be driven by 21st century technologies that provide high-efficiency, low-pollutant emissions, and low-cost electricity. CastleLight Energy is a ...
More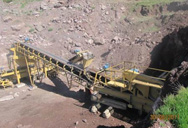
Coal Pulverizer – Power Plant Pall Corporation
6 天之前 In order to protect the coal pulverizer lube system components, Pall recommends maintaining a fluid cleanliness level of ISO 16/13 or better. This can be accomplished through the use of Athalon AS grade (ß12 (c)≥ 1000) or finer filters. Athalon, with their high particle removal efficiency and dirt-holding capacity, are ideally suited to cost ...
More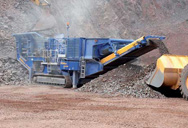
CFD Modeling of MPS Coal Mill for Improved Performance and Safety
2009.1.1 CFD modeling of MPS coal mill with moisture evaporation. Coal pulverizers play an important role in the functioning and performance of a PC-fired boiler. The main functions of a pulverizer are ...
More